The cost of pallets is influenced by a myriad of factors that you must navigate carefully.
A comprehensive understanding will allow you to make informed decisions that enhance your operational efficiency and drive profitability.
Let us talk about the factors that affect pallet costs.
Cost of Pallets: 6 Factors That Affect Pallet Costs
Material choices, design complexity, custom sizing, treatments and certifications, transportation logistics, and bulk ordering are among the factors that affect the cost of pallets.
Below are the explanations for each factor.
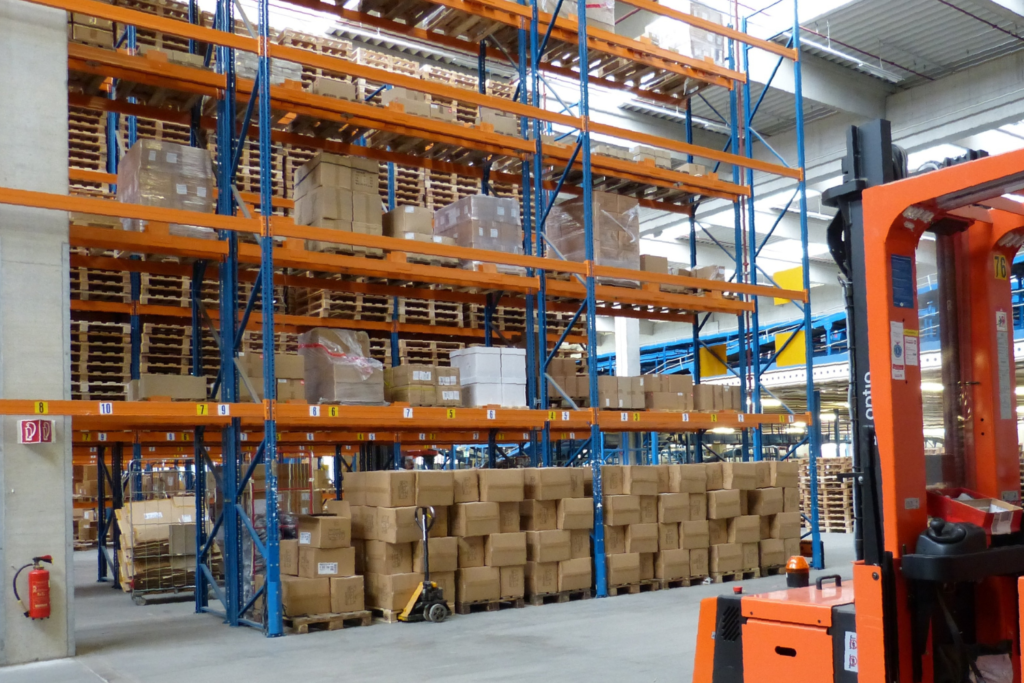
1. Wood, Plastic, and Metal Have Different Costs
Wooden, plastic, and metal pallets have cost structures that can significantly impact overall pricing.
Wooden pallets, for instance, are typically the most economical option. Their lower price point is largely due to the abundance of raw materials, as wood is widely sourced from forests and lumber mills.
However, the specific type of wood can greatly affect costs; hardwood pallets tend to be more expensive than softwood pallets due to their increased durability and strength.
Plastic pallets, while generally more expensive than their wooden counterparts, offer benefits such as resistance to moisture and chemicals.
The manufacturing process for them is more intricate, often requiring molds and higher energy input, contributing to their elevated costs.
Metal pallets, often made from steel or aluminum, are the most expensive due to the cost of materials and the complexity of their fabrication.
They are known for their durability and resistance to damage, making them suitable for heavy-duty applications, but their higher initial cost can be a barrier for some businesses.
2. More Complex and Durable Design Is More Expensive
More intricate designs, such as those featuring reinforced corners, advanced load distribution features, or added support beams, typically result in higher production costs.
You must assess your specific needs. A more durable design can be great for operations with rigorous handling requirements, but simpler designs may suffice for less demanding applications.
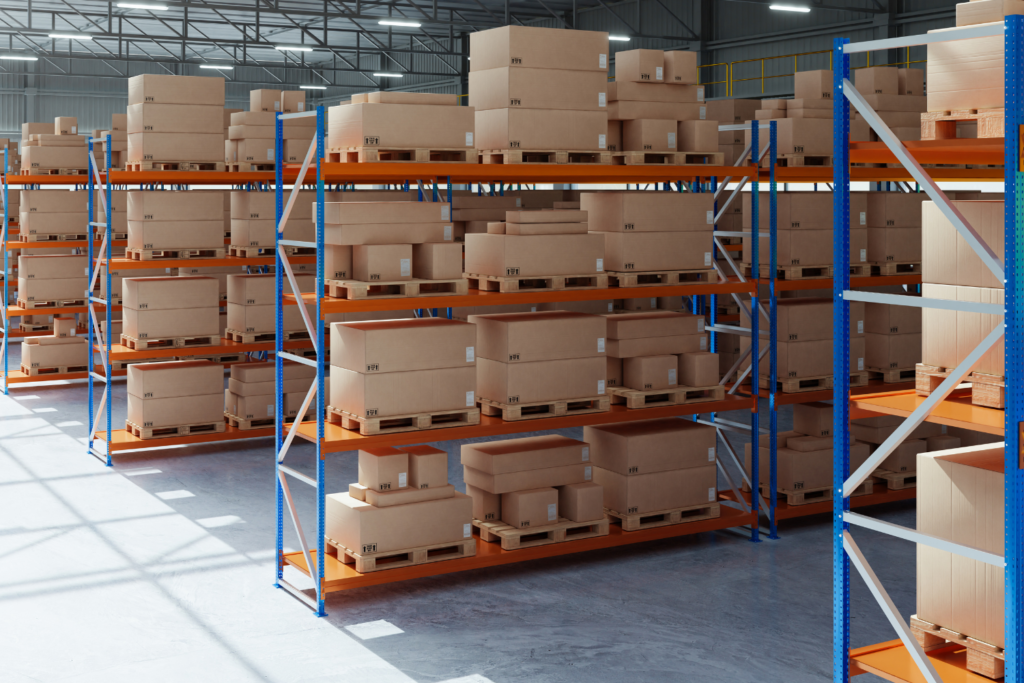
3. Custom Sizes Cost More Than Standard Sizes
Standard pallet sizes, such as the widely used 48″ x 40″ GMA pallet, are produced in high volumes and are therefore less expensive due to economies of scale.
However, if you require custom pallets to fit unique products or specific operational workflows, custom pallets may be a better choice. But it costs more.
Custom sizing introduces additional costs associated with specialized manufacturing processes, which can include unique tooling and longer production times.
4. Heat Treatment, Fumigation, and Other Certifications Are Not Free
Treatments such as heat treatment or fumigation are often mandated for compliance with international shipping regulations, particularly to prevent the spread of pests and diseases.
For instance, ISPM15 regulations require wooden pallets used in international shipping to undergo specific treatments, which adds a layer of cost.
Certifications themselves, while vital for regulatory compliance and market access, involve additional fees for testing and verification processes.
You must factor in these costs when determining the total expense of using wooden pallets, especially in global trade scenarios.
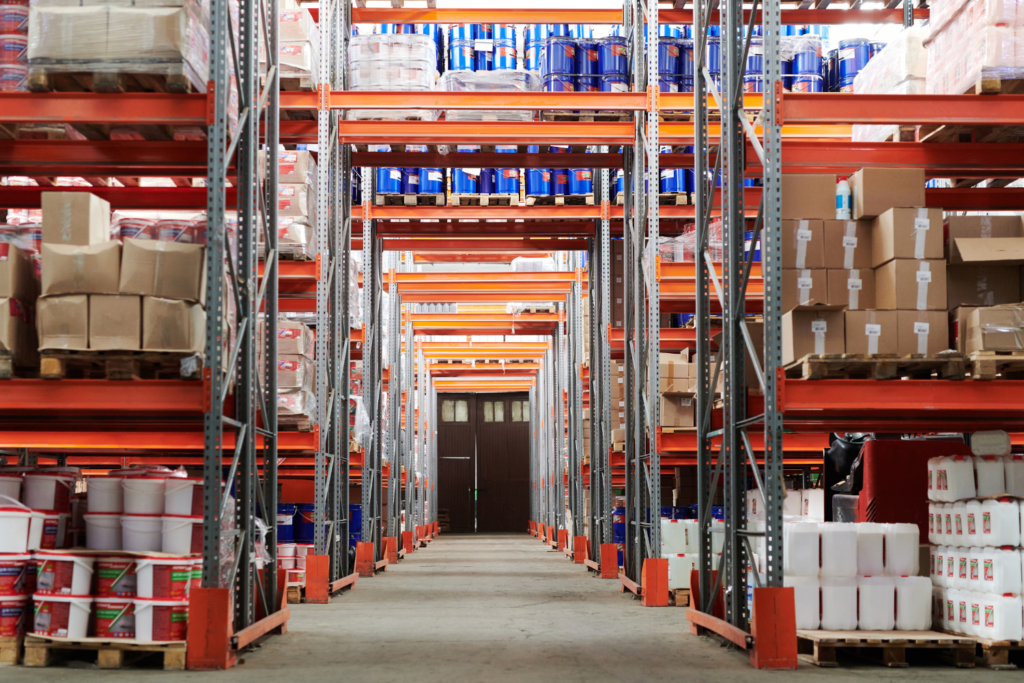
5. Transportation and Delivery Costs From the Supplier to the Customer Are Included in the Total Cost
Factors such as the distance between the manufacturer and the buyer, fuel prices, and chosen shipping methods all contribute to the expenses.
For example, a supplier located far from the buyer may necessitate higher shipping fees, which are typically reflected in the total cost of the pallets.
Logistical challenges such as fuel surcharges, shipping delays, and changes in freight rates can also further complicate budgeting.
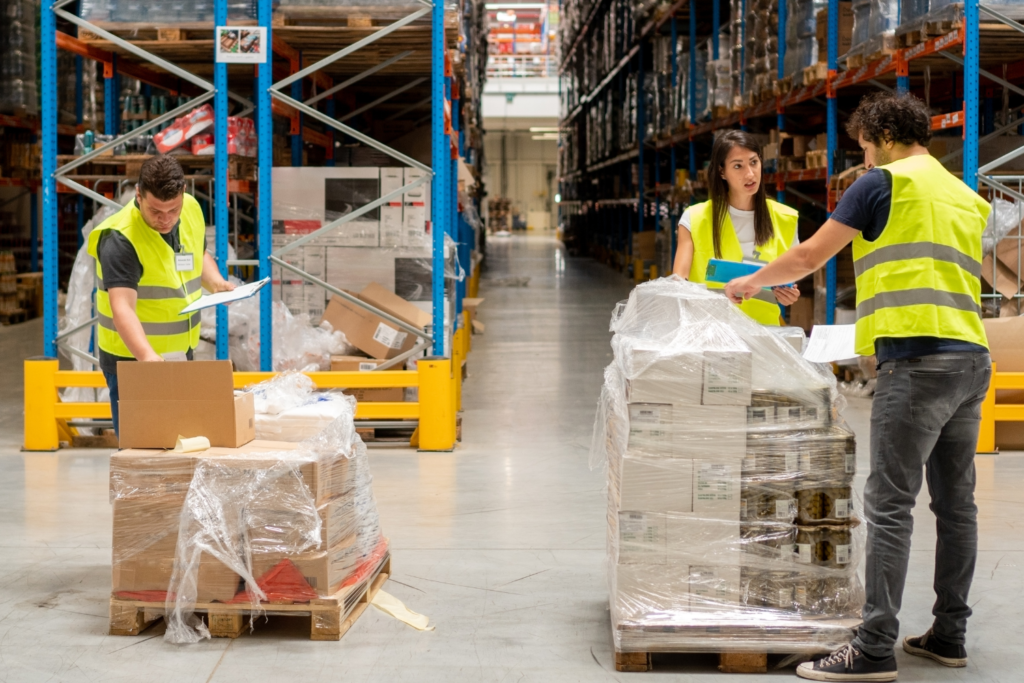
6. Bulk Orders Usually Reduce the Per-Pallet Cost
Ordering in bulk can lead to substantial cost savings. Suppliers frequently offer discounts for larger orders, as this reduces their per-unit production and shipping costs.
This can be an appealing option if you have sufficient storage capabilities and the ability to manage inventory effectively.
However, you must balance the advantages of bulk purchasing against your actual needs, as excessive inventory can lead to waste and additional holding costs if not managed properly.
Conclusion
The cost of pallets is influenced by a variety of factors. Carefully analyze each factor to strategically manage your pallet costs.
Materials, design complexity, custom sizing, treatment requirements, transportation logistics, and bulk ordering all contribute to the amount you will pay.
Contact us if you want to have an idea of how much pallets would cost considering your specific needs. You can also check out our pallet solutions here.
Chesapeake Pallets has been helping companies across the United States level up their logistics, one pallet at a time.
For inquiries, email info@chesapeakepallets.com or request a quote below!