Reverse logistics is about product returns, whether it be from customers to your business or from your business to the manufacturer.
Let us discuss reverse logistics and why you need to have a good strategy for it.
What Is Reverse Logistics?
Reverse logistics refers to the process of managing the movement of goods from their final destination back to their origin or another point in the supply chain.
It begins when products are returned to the retailer or the manufacturer, whether due to defects, dissatisfaction, or warranty claims.
In these cases, the retailer or the manufacturer must evaluate the condition of the returned items and determine the appropriate course of action.
Items that are defective may require repair or refurbishment, while those in good condition might be resold, donated, or redistributed.
Many companies partner with 3PL providers to manage reverse logistics operations more efficiently.
These providers offer expertise and infrastructure to handle returns, repairs, and recycling processes, allowing them to focus on their core competencies.
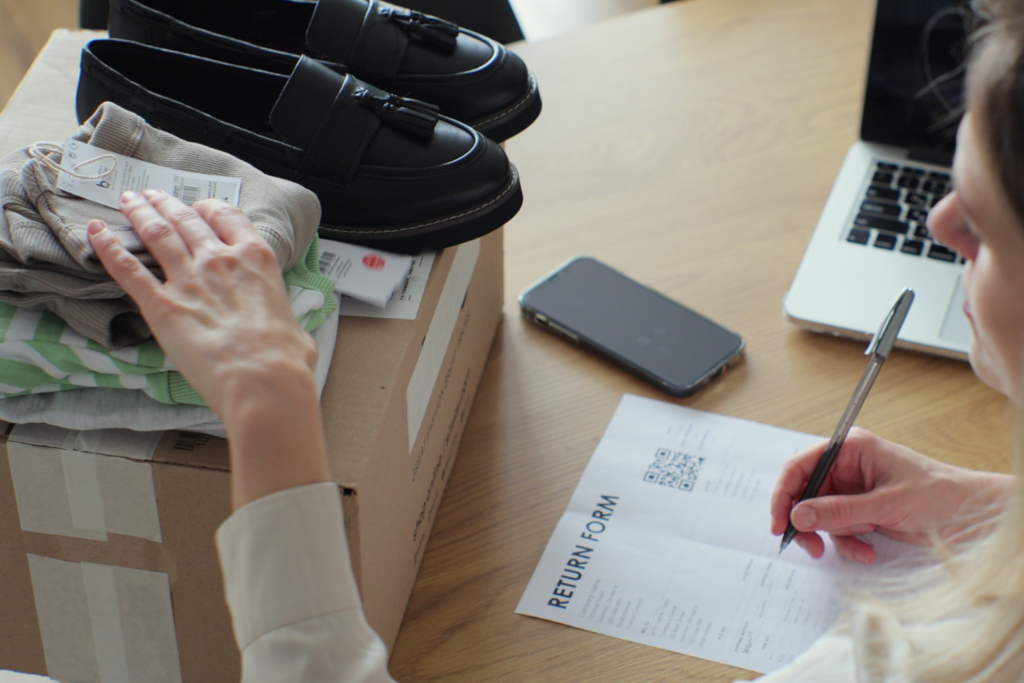
9 Different Types of Reverse Logistics
Reverse logistics is a comprehensive strategy that supports the circular economy, builds brand reputation, and drives long-term growth.
Below are the different types of reverse logistics.
1. Customer Returns
Customer returns are a central aspect of reverse logistics and involve the process of managing products that consumers send back to a retailer or manufacturer after purchase.
These returns occur for various reasons, such as defective goods, dissatisfaction with the product, incorrect orders, or changes in consumer preferences.
2. Retailer Returns
Retailer returns involve the reverse flow of goods from retailers back to manufacturers or distributors, often because of unsold inventory, seasonal overstock, or damaged products.
Unlike customer returns, these are typically managed on a larger scale and can be more predictable, as they are often governed by prearranged agreements.
3. Product Recalls
Product recalls occur when a company retrieves defective or potentially hazardous products from the market to ensure consumer safety and compliance with regulations.
They can arise from design flaws, manufacturing errors, or safety concerns discovered post-sale.
Examples include automotive recalls due to faulty airbags or food recalls caused by contamination.
They are often mandated by regulatory authorities but can also be initiated voluntarily by companies to protect their reputation and prevent liability.
4. Repairs and Maintenance
Repairs and maintenance are reverse logistics processes that focus on restoring the functionality of products that have been damaged, malfunctioned, or worn out.
These activities are particularly common in industries with high-value, durable goods, such as electronics, machinery, or automotive components.
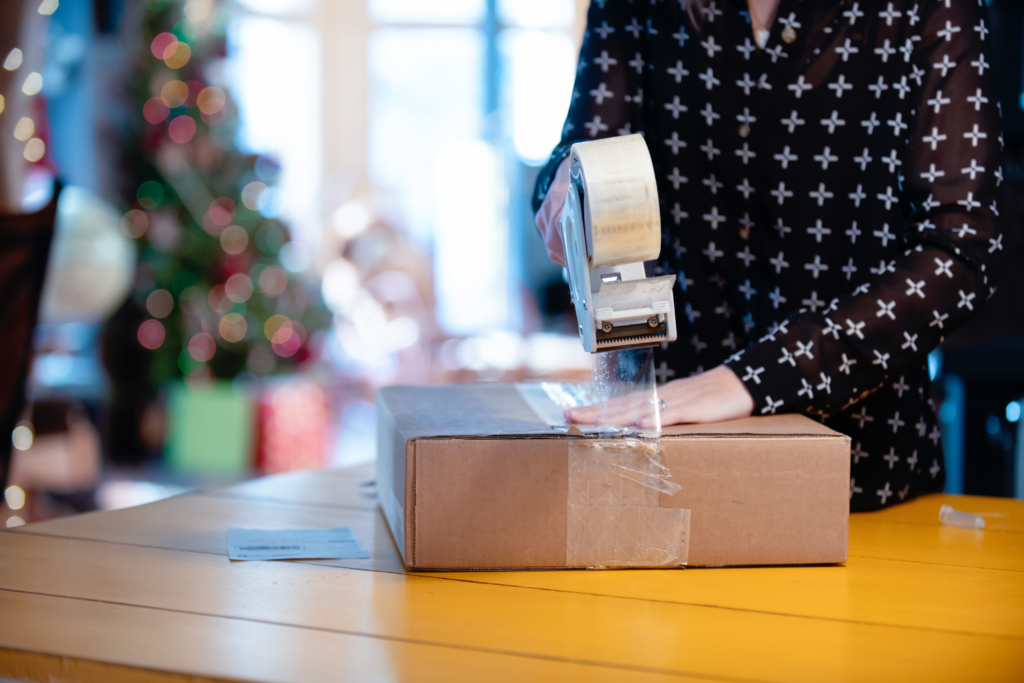
5. Recycling and Disposal
Recycling involves breaking down products into their raw materials, such as metals, plastics, or glass, which can then be reused in manufacturing.
Disposal, on the other hand, is reserved for materials or products that cannot be reused or recycled.
Companies can implement take-back programs to encourage consumers to return old or unwanted products for proper recycling or disposal.
6. Refurbishing and Reconditioning
Refurbishing and reconditioning involve restoring used or damaged products to a condition where they can be resold or reused.
These processes are critical in industries such as electronics, furniture, and automotive, where there is significant value in extending the life of a product.
7. Remanufacturing
Remanufacturing is a specialized form of reverse logistics that involves completely rebuilding a product to meet or exceed its original specifications.
This is common in industries where products are designed for long-term use and high-value components can be recovered and reused.
8. Packaging Recovery
Packaging recovery involves the retrieval, reuse, and recycling of packaging materials such as cardboard boxes, pallets, and plastic containers.
This aspect of reverse logistics is increasingly important as businesses seek to minimize waste and reduce the environmental impact of their operations.
9. Asset Recovery
Asset recovery refers to the process of identifying and recapturing value from unused, surplus, or obsolete assets, such as machinery, equipment, or inventory.
This process is particularly important for businesses that regularly update technology, relocate operations, or discontinue product lines.
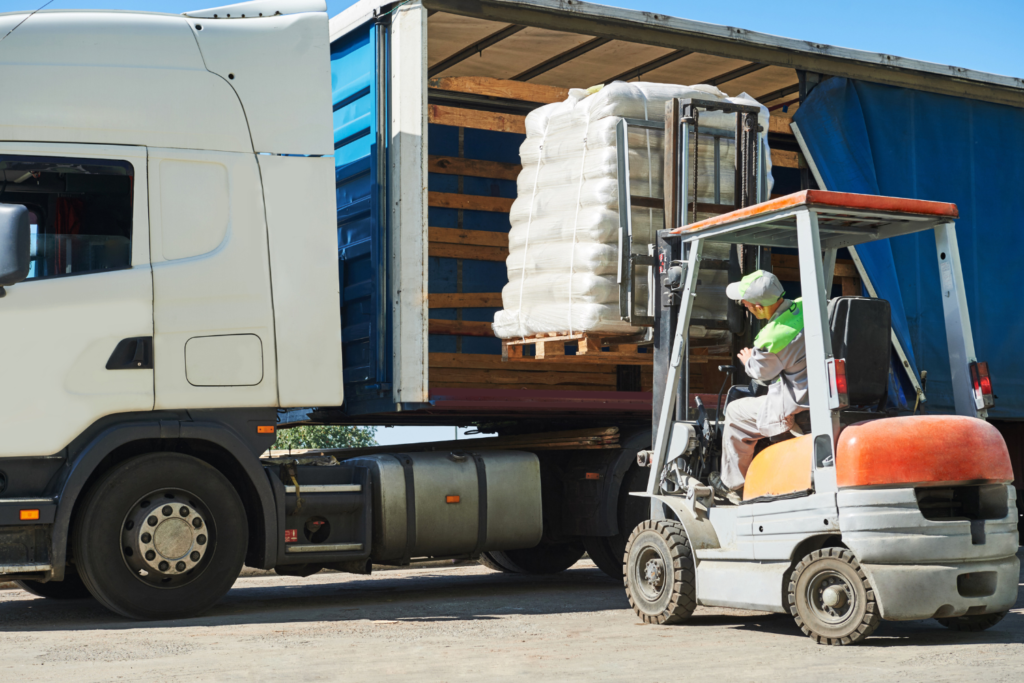
How Does Reverse Logistics Affect Your Business?
Reverse logistics matters because it impacts profitability, sustainability, and customer relationships. Below are specific ways it could affect your business.
1. Reverse Logistics Helps Manage Inventory by Dealing with Excess and Obsolete Stock
Excess inventory often arises from overproduction, inaccurate demand forecasting, or seasonal changes.
On the other hand, obsolete stock results from technological advancements, changes in consumer preferences, or the expiration of product lifecycles.
Through reverse logistics, you can create pathways to handle these issues efficiently.
For example, unsold inventory may be redistributed to secondary markets, donated to charitable organizations, or repurposed into new products.
Items with no further use can be disassembled to recover valuable components, reducing waste and extracting residual value.
2. A Streamlined Return Process Can Improve Customer Satisfaction and Loyalty
A streamlined return process increases customer satisfaction, particularly in sectors where consumers expect flexibility and convenience.
It easily builds trust, enhances the shopping experience, and fosters long-term loyalty.
Take the time to analyze return data so that you identify common pain points, such as defective products or misleading product descriptions.
You can reduce future returns, improve product quality, and better align offerings with customer expectations if you address the issues.
3. Feedback From Returned Products Can Be Used to Improve Product Quality and Reduce Future Returns
Each return tells a story, offering insights into design flaws, manufacturing defects, or mismatches between consumer expectations and product performance.
By examining these returns, you can identify patterns and implement targeted improvements, which enhances product quality and reduces future returns.
4. Reselling Refurbished or Recycled Products Can Create Additional Revenue Streams
Reverse logistics enables you to create new revenue streams by refurbishing or recycling returned products for resale.
This practice is valuable if your products have a long lifecycle or high residual value, such as electronics, furniture, and appliances.
You can extract additional value from items that might otherwise be considered waste.
5. You Can Maximize the Recovery of Valuable Materials From Returned Products, Reducing the Need for New Raw Materials
One benefit of reverse logistics is its ability to maximize the recovery of valuable materials from returned products, reducing the need for new raw materials.
When products reach the end of their useful life or are returned due to defects, they often contain materials that retain significant value.
If you integrate advanced sorting and recycling technologies into your reverse logistics processes, you can achieve higher recovery rates.
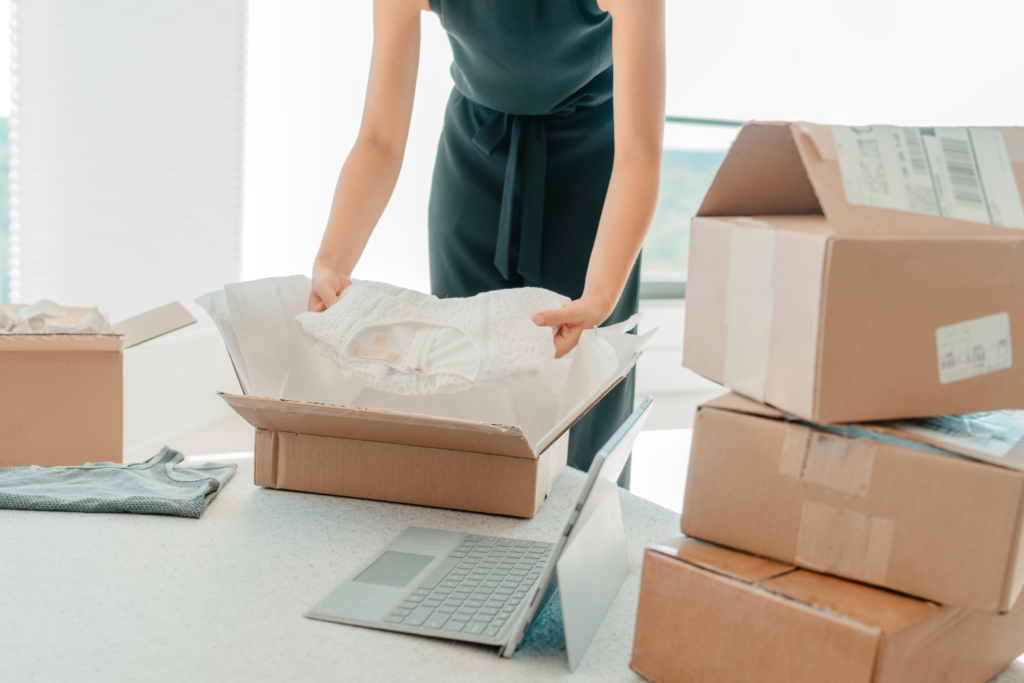
Conclusion
Traditionally, logistics focused on the movement of goods from manufacturers to consumers, with little consideration for what happens once products reach the end of their life cycle or if they are returned.
However, the growing importance of sustainability, cost management, and customer satisfaction has elevated reverse logistics to the forefront of business strategy.
Check out our services here if you need logistical assistance.
Chesapeake Pallets has been helping companies across the United States level up their logistics, one pallet at a time.
For inquiries, email info@chesapeakepallets.com or request a quote below!